Traffic management delivers milk efficiency (Jan 25)
- CowManagement
- Feb 5
- 6 min read
A mix of free-access and guided robot-milking systems is helping to drive dairy productivity on one Cumbria-based unit. So how do the two setups differ and how do they work?
TEXT REBECCA BARNINGHAM & RACHAEL PORTER
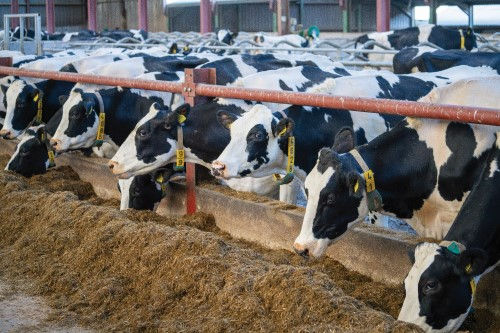
Two different robotic milking setups are helping one Cumbria-based dairying family to perfect their day-to-day and longer term herd management. David Armstrong manages his family’s 315-cow herd, plus 300 followers and a further 300 head of beef cattle, alongside his brother Andrew, father Harold, and uncle John. The 265-hectare unit, based at Bromfield near Wigton, recently hosted an open day to showcase its two robotic systems.

The family first made the switch to robotic milking in 2019, installing four GEA robots to milk high-yielding cows using a typical free-access setup. The lower yielders continued to be milked, twice a day, through the unit’s 28:28 herringbone parlour.
Two sheds, each with two robots, were converted to house the high-yielding cows and allow the herd to be grouped by lactation while fresh. This free-access system made use of existing buildings, with heifers housed in older cubicles with smaller dimensions. “Grouping heifers separately from cows at the start of lactation helps to reduce competition and bullying, and maintain their production at 82% of the cows’ level.
Robotic investment
Pleased with robot and herd performance, the Armstrongs invested in a further three GEA DairyRobot R9500’s in February 2024. This required building a new shed with 140 cubicles and presented the family with a different opportunity – to opt for a guided traffic system with a ‘milk first’ configuration. In order to reach the feed barrier, cows must pass through a selection gate.
If a cow has ‘milk allowance’ she is then milked before being given access to the feed area. “The key benefit of this system is to reduce the labour requirement for ‘fetching’ late-lactation cows in to be milked,” says David. “And it also improves robot-use efficiency.”
Grouping late-lactation cows together also allows body condition scores to be monitored and managed, and the system has also allowed David to reduce concentrate feed rate, down to just 0.1kg per litre, through the robots.
Across both systems, cows visit the robots, on average, 2.7 times a day. David says that automating milking has also pushed up average daily milk yield per cow by at least seven litres, to between 37 and 40 litres. “When milking through the conventional parlour, we were unable to push through the 30-litre barrier.”
Free-access system
The all-year-round calving herd is currently averaging 11,000 litres, at 4.50% butterfat and 3.45% protein, with a somatic cell count of 120,000 cells/ml. Milk is sold to Arla on a supermarket contract.
Free flow or free access allows cows to move freely to the robot, feed fence and cubicles. All cows have access to the robot whether they are ready to be milked or not. It is a cost-effective configuration that’s easy to install in an existing shed, but directing fresh cows to the robot can be time-consuming.
Guided traffic systems direct cows to a sort gate, which either allows or prevents access to the waiting area for milking. This system costs more than the free-flow setup, but cow management can be organised on an ad-hoc basis, without wasting time or requiring additional resources.
So, how do the two robotic systems compare? David says they both have their place on the unit. “Both work well – we have no complaints. The guided system works best for the mid- and late-lactation cows – they’re already in their lactation rhythm and will get up to eat and, therefore, pass through the robots to be milked first. And there are no ‘time wasting’ passing visits from cows not due to be milked,” he explains.
Conversely, the free access better suits the fresh cows and heifers, and the early-lactation group, which typically comprises around 178 head. “They’re able to visit the robot and then return directly to cubicles to rest, or go and eat – there’s choice.”
With free access, cows are able to get familiar with the setup and, if needed, one of the team can step in, when alerted, and ‘fetch’ any cows or heifers needing encouragement to be milked.
“Milking through a conventional parlour may have given us sight of every cow, twice a day, but essentially we were just looking at her rear end and udder – not the whole animal. We’ve more time to actually observe the herd, particularly in the free-access system.”
And there’s less stress for the herd. “It’s a quieter way to manage and milk cows – there’s far less noise and we’re not ‘interrupting’ the cows twice a day to put them through a conventional parlour. In fact, even though we’re handling the cows less, they’re much calmer when we walk through the sheds, and easier to work with.”
David has also noticed that even the more timid cows in the herd are still keen to get up and eat or be milked.
“There’s less competition – particularly in the guided setup – and fewer ‘bully’ cows pushing their way in, and this means less stress.”
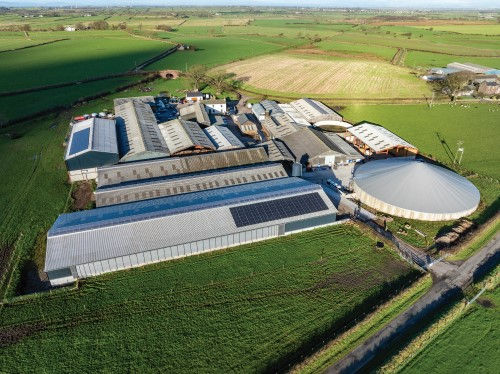
Individual-cow management
The automatic milking system has also benefitted the dairy team by providing more data, particularly on individual cows. “Uncle John wanted to take a step back from the business, and that meant one less set of eyes on the cows. We knew we needed to find a way to keep a close watch on individual-cow health, fertility and performance without putting more pressure on our already heavy work load,” explains David.
GEA’s herd management system, called Dairy Net, was added in 2019. “Its design makes it easy to use and navigate, and it’s linked to a mobile app for ‘cow-side’ management, which is really handy.
“It offers pre-set lists and data analysis tools, as well as performance analysis for robot and milking parameters.
There’s a ‘one-click’ cow information page, which we find particularly useful, and it also has a ‘multi-animal selection’ feature to help us when planning and performing herd management tasks.”

They also invested in a feed pusher – a GEA DairyFeed F4800 – in 2019. “It seemed logical when we invested in the first robotic setup, helping to complete the automated management of the shed,” explains David, who says it gets on with its job, unnoticed by the cows. “That said, I’ve seen that when the cows hear the feed pusher whirr into action that they steadily get up and walk to the feed fence – almost on cue.
“I’ve been up in the dairy office, which overlooks one of the sheds, and seen maybe 10 cows in the feed passage. I can look up again a few minutes later – once the robot has made its pass – and see 30 cows stood eating.”
The herd is fed a grass-silage based TMR, which also contains wholecrop wheat grown on the farm.
He says that frequent feed pushes – he has it set to push up TMR every two hours – increases the number of cow visits to the feed barrier.
This supports higher and more consistent dry matter intake, which also plays a role in increasing milk yields, improved cow health and greater profitability.
“It’s also helped to minimise feed waste and feed sorting,” says David. “And there’s not a mad rush to get to the feed, which reduces competition at the barrier.” David says that one of the most asked questions from visiting producers during the open day was ‘which robotic system is better – free access or guided?’.
“For us, I’d struggle to choose between the two as both suit particular cow groups. But if I had to pick one I’d go with guided. It saves a little more on labour and robot down time.
“They’re both great systems and are certainly helping us to run and build a more sustainable business that will be fit for the future,” adds David.
“The next generation of Armstrongs are too young to be thinking about a future in dairying. But we’d like to develop a business that could support them if they decide to take that route.”
Comments